领克汽车:智破节拍瓶颈,数智向“新”奔腾
走进领克汽车张家口工厂,我们会看到这样一幅充满科幻感的自动化生产图景:AGV小车在厂区内有序穿梭,将生产物料高效配送到指定地点;挥舞的机械臂根据生产需求来回摆动,短短数秒就将座椅、轮胎等组装到位。在这里,平均每90秒就有一辆新车下线。90秒,几乎只相当于做几个深呼吸冥想放松的时间。
领克张家口工厂是吉利汽车集团和沃尔沃汽车集团合资在张家口建设的整车工厂,也是中国北方最大的整车制造基地之一,主要生产领克03、领克03+等车型,年产能12万辆。自2018年上市至今,累计产销整车58万辆,实现工业产值707.9亿元。然而,如今欣欣向荣的生产成果背后,在2023年,领克张家口基地一度面临着严峻的技改挑战。而针对诸多痛点和桎梏,领克汽车与中兴通讯、中国移动河北公司及吉速物流积极合作,在此成功落地了5G智能配送项目,划定了数智时代向“新”奔腾的起跑线。
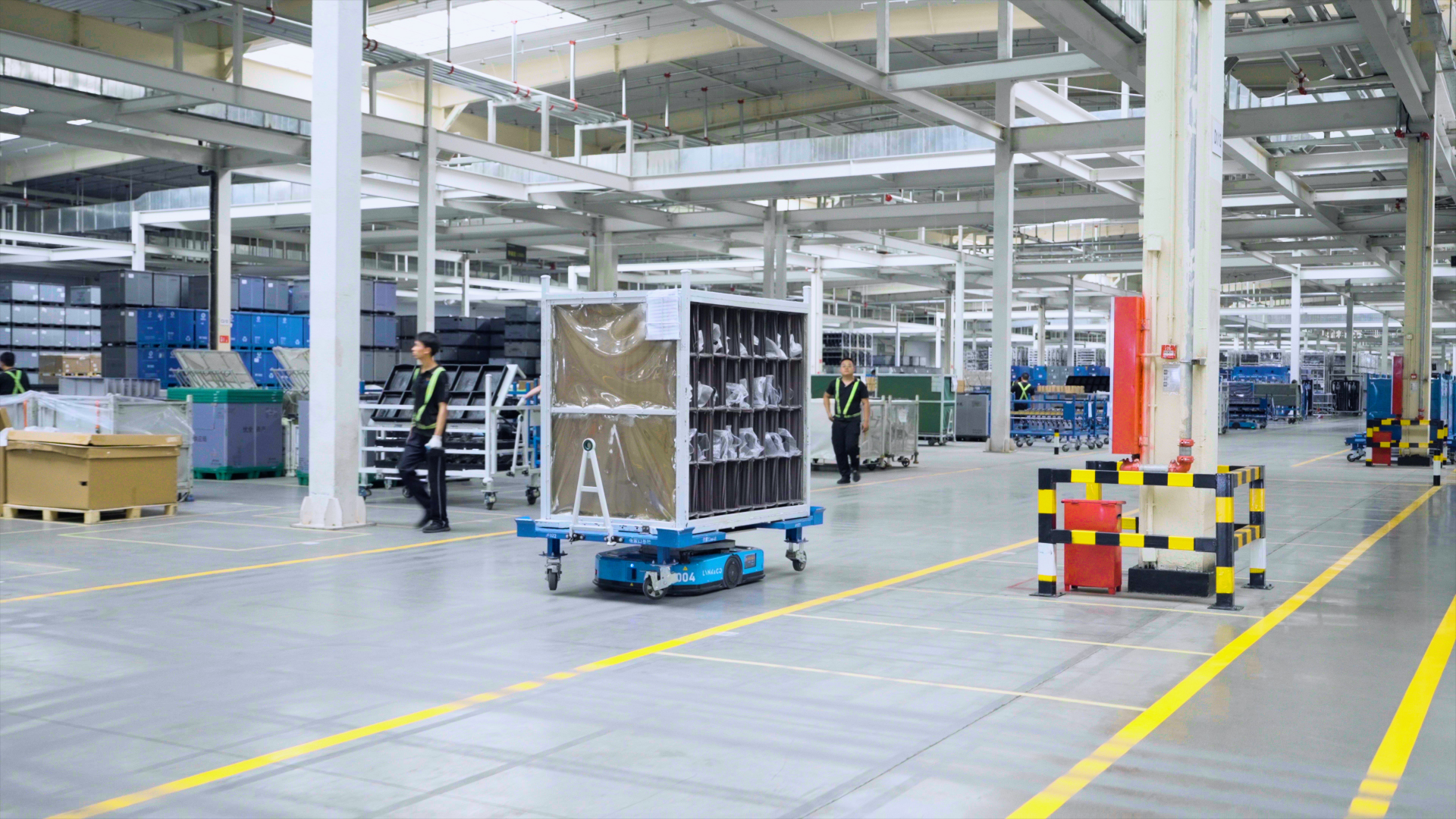
不破“瓶颈”便不立:激发数智化转型的决心
在汽车行业中,生产节拍是衡量制造效率的关键指标。激发领克张家口基地数智化转型决心的,正是节拍需求大提升、多车型混线生产、现有Wi-Fi信号差这三大生产桎梏。其一,目标计划产能接近成倍提升,亟需消除工序中广泛存在的“节拍瓶颈”,而人工配送会导致成本翻倍,无法满足工厂提速增效的愿景。其二,多车型混线生产意味着物料数量明显增多,由4000种需求物料增加至6500种物料,传统的地磁、二维码导航AGV及器具管理方式等已无法满足产线的高效运行。其三,Wi-Fi种类多、信号差,总装车间为二层钢制厂房,网络设备布放在二层,业务在一层,中间受钢制材料屏蔽影响,导致信号弱、丢包严重,且车间Wi-Fi因业务需求不同而重复部署,出现干扰严重的问题,难以满足高节拍生产需求。
为了应对这些挑战,中兴通讯携手中国移动河北公司助力领克汽车打造了5G智能配送项目。该项目为领克汽车“量身定制”了一张5G车企专网,并在此基础上实现了全国首个5G激光SLAM导航AGV在老旧车厂复杂环境下的大规模应用,显著提升了总装车间物料配送效率,确保了技改后生产线能够满足接近翻倍的高节拍生产需求。
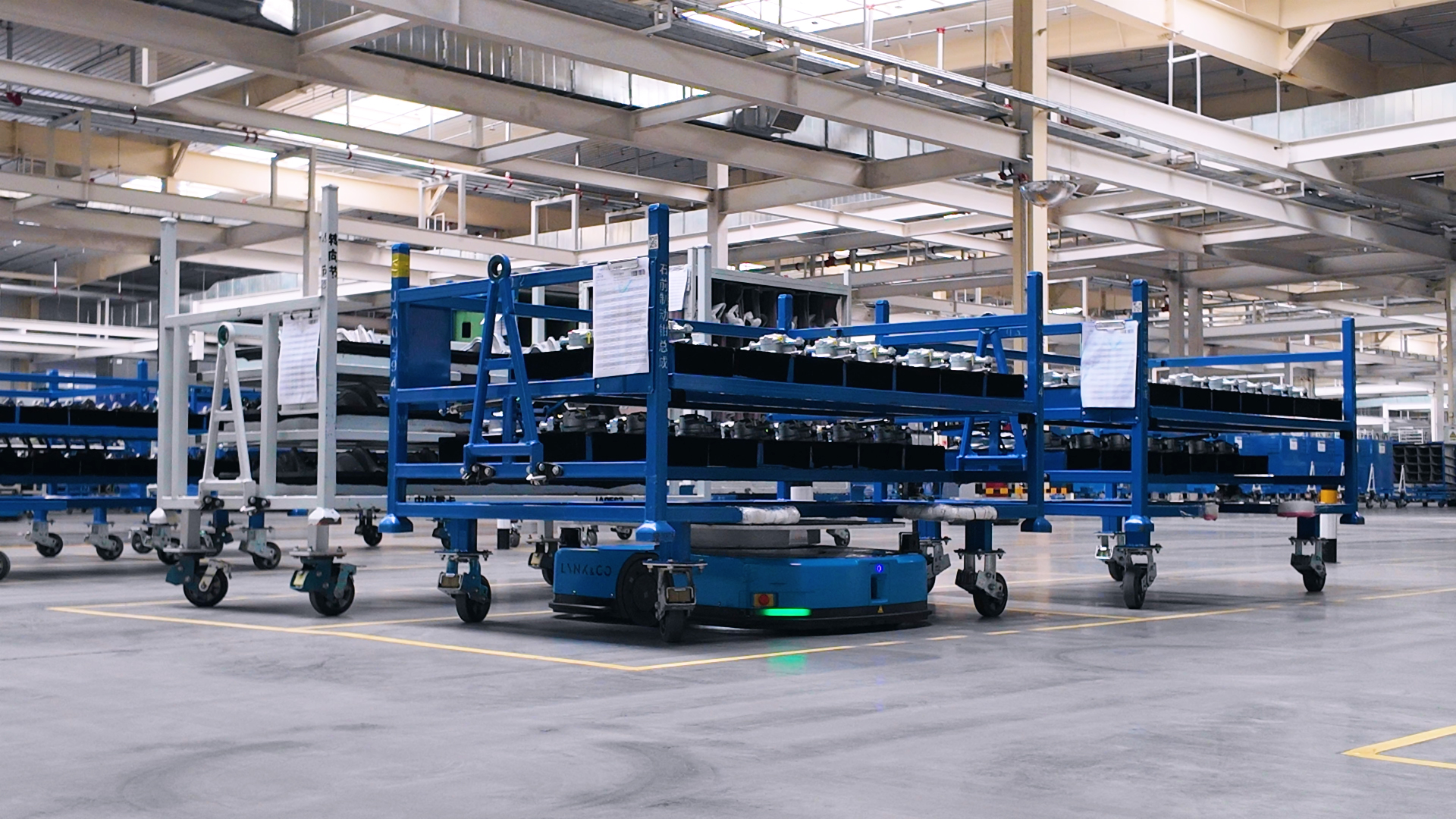
高效运转之“妙方”:5G+新质生产力的担当
“每90秒就有一辆新车下线”的造车速度,无疑要求每条生产线都高度互联并协同作业,以统一的节拍进行高效运转。而支撑高效协同作业、培育汽车产业新质生产力的,正是5G+数智技术。
首先,5G确定性网络保障了特定业务的确定性网络需求,实现AGV行驶区域稳定无丢包、无卡顿,避免交通管制失效、异常告警不及时等情况发生。同时,调度平台基于5G工业边缘云部署,能够进一步助力AGV设备丝滑协同。其次,中兴通讯AGV调度系统与吉利集团吉易达、GLES系统配合,达成物流全域管理,在保障及时按需供货的同时,实现线边无冗存的精准配送模式。最后,自然导航技术弥补了磁条和二维码易污染损坏的缺陷,车辆本体的6大核心传感器开发了包括动态区域检测、置信度自适应变更、地图擦除等在内的多项技术功能,使5G自然导航AGV在环境频繁变化的总装车间中能进行高精度自主导航和智能冲突解脱,无需借助二维码、地磁等导航标识即可完成物料资源定时定点定量配送。
在智慧物流、视觉防错等5G工厂应用场景中,领克汽车深切感受到了5G智能化改造所带来的直观效益。目前,领克汽车张家口工厂已在超过5万㎡的总装车间内部署31台5G AGV,实现厂区21种物料周转场景的无人化。相较引入方案前,总装物流车间成本降低数百万/年,物流效率及时性提升33%。而在焊装车间,600余台机器人能精准完成前底盘、后底盘、发动机舱等点位的焊接,自动识别零件并全自动制造,确保整个车身5000余个焊接点的牢固强度完全一致。当不同型号车体生产切换时,可自主驱动工位卡槽实现生产换线,解决线缆磨损问题,赋能柔性化生产,有效提升焊接效率。焊装车间自动化率达75%以上,主焊线自动化程度100%。
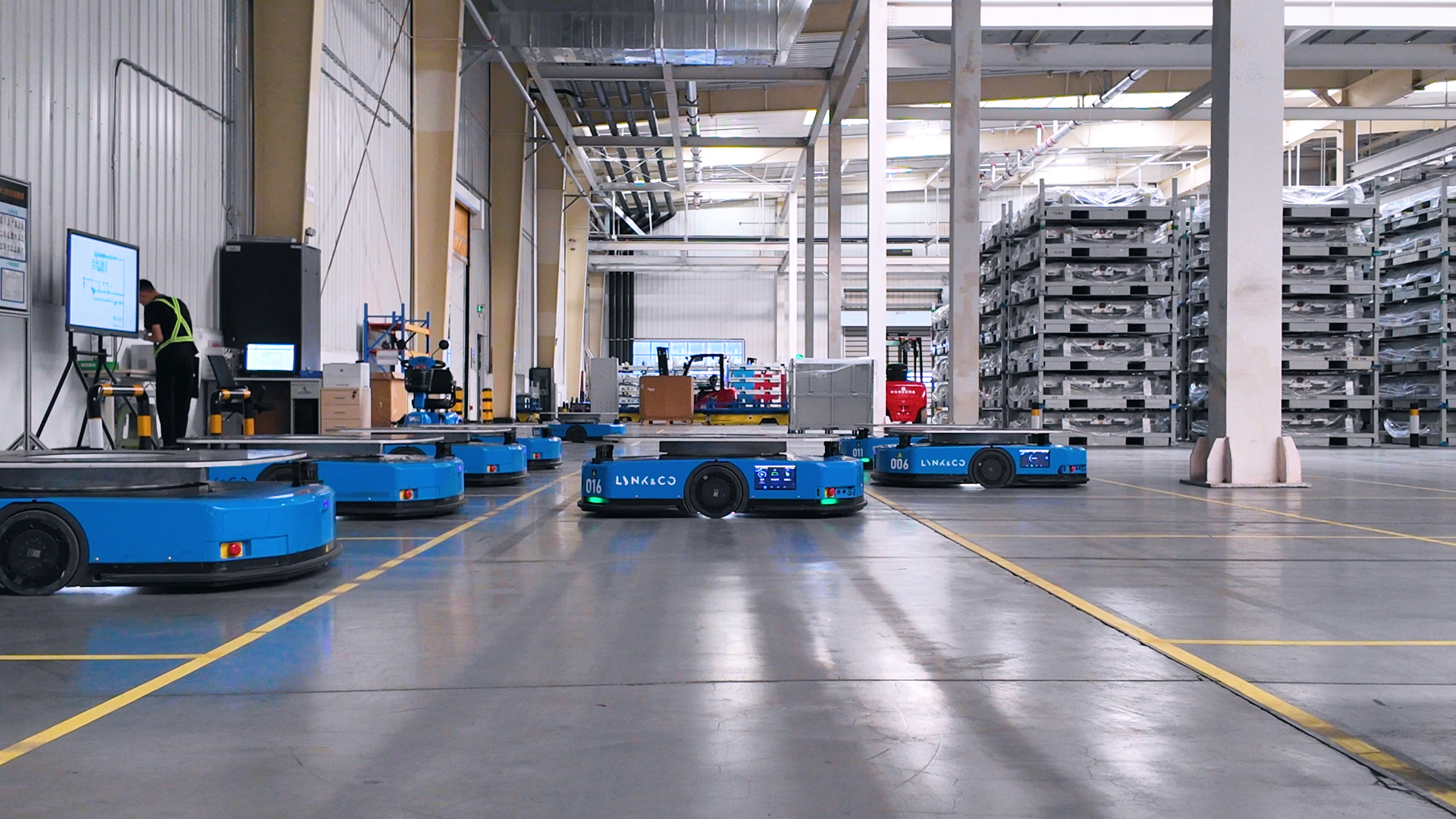
汽车产业是大国经济的“压舱石”,将5G+数字技术融入传统生产环节,不仅是领克汽车积极发展新质生产力、扎实推进高质量发展的鲜明呈现,也是汽车产业高端化、智能化、绿色化发展的必然趋势。面向未来,中兴通讯也将联合更多产业伙伴,持续深化生产、质检、物流等业务场景应用领域合作,将5G+数字技术融入传统生产环节,助力千行百业打造数智化转型业界典范。