Smart Steel: 5G Fully Connecting WISCO Factory
Wuhan Iron and Steel Corporation Limited (WISCO), a pivotal steel manufacturing base under China Baowu Group, operates with a world-class steel production process. The company produces a diverse range of products, encompassing over seven major categories and more than 500 varieties, boasting a production capacity exceeding 15 million tons. In light of increasingly stringent environmental policies and the carbon peak and carbon neutrality goals, WISCO has introduced its "Four Uniform Strategies" and "Three Integrated Approaches" for smart manufacturing. Through combining 5G networks with informatization and intelligent construction of steel industry, WISCO aims to seamlessly integrate production, technology, equipment, and management. This strategic integration is designed to enhance production efficiency while reducing operational costs.
WISCO, together with China Unicom and ZTE, has joined efforts to lead to the establishment of the "5G Fully Connected Smart Steel Factory" project. This project has now evolved into the largest 5G private network in the steel industry worldwide, achieving an impressive 99% 5G coverage within the factory premises. Leveraging this robust 5G private network infrastructure, the project has deployed 25 steel applications across six major scenarios. These applications span intelligent logistics, production control, digital equipment management, energy and environmental control, quality control, and safety management. To streamline operations, the factory has established a company-level control center along with dedicated operation centers for iron making, steelmaking, CSP, and hot rolling. This integrated approach has paved the way for a seamless, all-in-one-click steelmaking process.
5GC Empowers Smart Manufacturing
In 2021, the implementation of exclusive 5G core network coverage was initiated in WISCO. Technologies such as 5G private networks, edge computing, and network slicing were leveraged to empower intelligent manufacturing. Using smart factories as the platform and focusing on the intelligent transformation of key manufacturing processes, WISCO has realized its operations on end-to-end data flow supported by 5G networks. This approach has enabled innovative applications in the 5G + industrial field network. Operations are now centralized off-site, equipment maintenance and monitoring are carried out remotely, high-risk work environments are managed by robots, and services have all been moved online.
In 2022, 5G networks fully met the unmanned shipping needs of WISCO's steel factory. Tailored to different operational scenarios in production, WISCO established industrial control private networks across various plants. Leveraging its 5G industrial computing power infrastructure, ZTE provided an integrated solution that combined "end," "edge," "cloud," "network," and "industry," complemented by end-to-end business connection monitoring. This initiative was further bolstered by practical efforts across multiple dimensions, including production centralized control platforms, digital mobile operation platforms, intelligent environmental management, and safety production, aiming to significantly enhance WISCO's production quality, reduce costs, and boost efficiency.
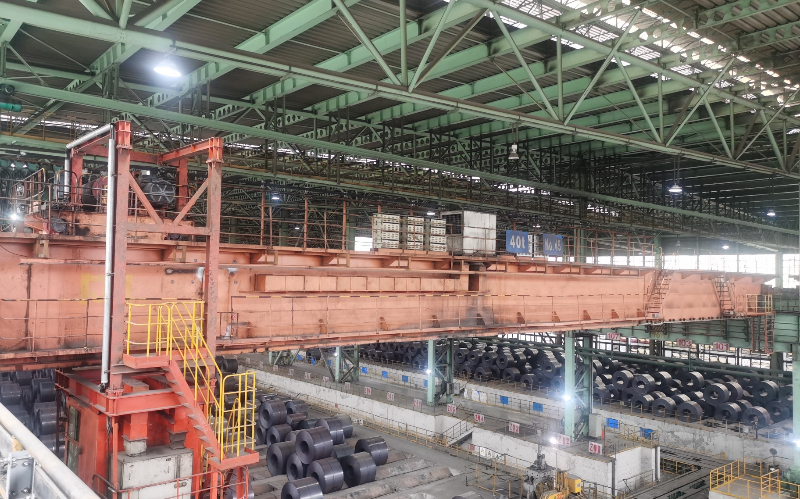
Based on the high bandwidth, low latency, and broad connectivity features of the 5G network, the 5G core network has been strategically deployed to accommodate six major categories and 25 types of applications. These applications encompass smart logistics, production control, and digital equipment management, among others. Control centers have been established for ironmaking, steelmaking, CSP, and hot rolling, achieving centralized operations away from the site and integrated, real-time data collection.
Empowered by 5G, WISCO has seen a 19% overall improvement in efficiency, a 10% reduction in energy consumption, and a 23% decrease in labor costs, marking the beginning of a new journey towards high-quality development.
5G+Smart Management Platform
The iron-steel interface plays a crucial role in linking the ironmaking and steelmaking processes in steel manufacturing. In traditional operations, information collection relies on manual offline methods, often leading to 'information silos' between different units. Planning is done using physical models, and production scheduling depends on phone calls. With the introduction of the 5G+ internet system, the entire process now benefits from centralized online management of real-time intelligent status information. Especially in transportation, 5G empowers centralized control of railway dispatching, streamlining it to a 1+1 model. With unmanned locomotive operation, functions like automatic coupling and decoupling, parking, and charging are now automated.
Additionally, leveraging big data analytics, logistics and transportation processes are visually tracked and controlled, enabling deep analysis of comprehensive logistics cost data. Utilizing a combination of 5G, sensors, AI, and AR technologies, a range of advanced features in railway and logistics management have been implemented. These include automatic triggering of alarms at railway crossings based on locomotive location information, video-based alerts for obstacle intrusions at crossings, and remote control capabilities for both locomotives and unloading machinery via live video feeds. Additionally, drones were employed for inspections along railways and within factory roads. Furthermore, environmental monitoring of vehicles within the facility was also conducted, showcasing the comprehensive integration of these cutting-edge technologies to enhance efficiency and safety.
Data shows that since the comprehensive launch of the 5G+ internet iron-steel interface system, it has helped WISCO optimize work for 20% of its employees, boosted molten iron transportation efficiency by 10%, and reduced the temperature drop of molten iron by 10°C. Preliminary estimates indicate that the direct economic benefits saved from transportation alone amount to over 40 million RMB annually.
Embracing a New Era of Smart Manufacturing
Pioneering the 'ALL IN ONE' smart manufacturing approach, WISCO has set up control centers for ironmaking, steelmaking, CSP, and hot rolling. This centralization allows for remote operation and real-time data collection, making features like 'one-click steelmaking' and 'smart transportation' a reality. As a crucial steel production base for China Baowu, WISCO is ushering in a new era of smart manufacturing, leveraging 5G and industrial internet technologies to embrace the 'cloud computing' and 'dream factory' vision.
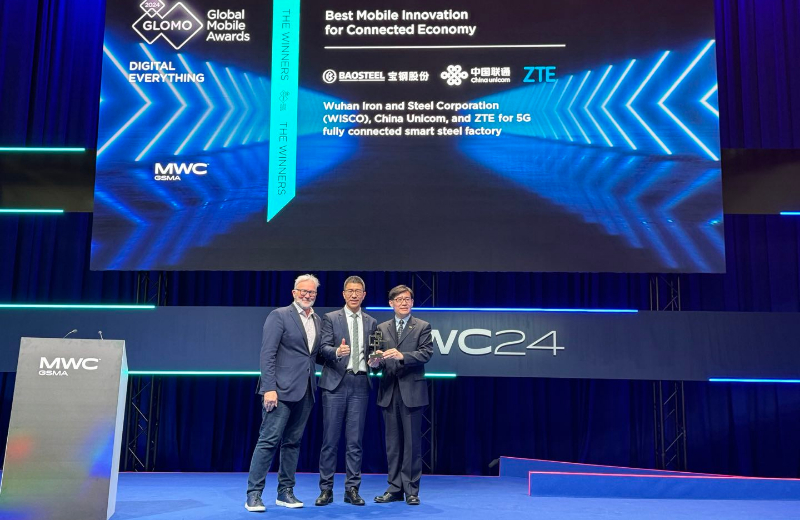
The joint project "5G Fully Connected Smart Steel Factory" earned the "Best Mobile Innovation for Connected Economy" at the Global Mobile (GLOMO) Awards during MWC Barcelona 2024.